The fuel system is fascinating, to say the least. It is a system that contains a lot of parts that all work synchronized in order to deliver fuel to the engine continuously.
I always wanted to learn more about fuel systems and how they work. So, I did some research online and talked to couple a of mechanics, and here is what I’ve learned.
Key Takeaway
- Fuel systems in vehicles can be broadly categorized into two types: carburetor systems, which mix fuel and air in a carburetor before the mixture enters the engine, and fuel injection systems, where fuel is directly injected into the engine’s combustion chamber or intake manifold.
- The main components of a fuel system include the fuel tank (stores fuel), fuel pump (pumps fuel from the tank), fuel filter (removes impurities from the fuel), fuel injectors or carburetor (mixes fuel with air and delivers it to the engine), and the ECU or carburetor controls (regulate the amount of fuel delivered based on engine performance needs).
Types of Fuel Systems
There are two types of fuel systems used in most vehicles. They are very similar, however, they deliver fuel in slightly different ways.
1. The return-type of fuel system
The return type fuel system components are:
- Fuel tank
- A fuel pump
- Fuel lines
- A fuel filter
- Fuel rail with injectors
- Pressure regulator
- Return line
On a return-type fuel system, the pressure regulator is located on the fuel rail. Once upon a time, gravity moved the fuel from a vehicle’s tank to the carburetor. Today’s program fuel injection system needs to have a pressurized and constant supply of fuel delivered to the injectors at all times. The supply of this constant pressurized fuel is enabled by the fuel pump.
2. The returnless type of fuel system
The returnless type of fuel system has the following components:
- A fuel tank
- Fuel pump
- A fuel filter
- Pressure regulator
- Fuel lines
- Fuel rail with injectors
On a returnless fuel system, the pressure regulator is located inside the fuel tank.
Fuel System Components and How They Operate
1. Fuel Pump
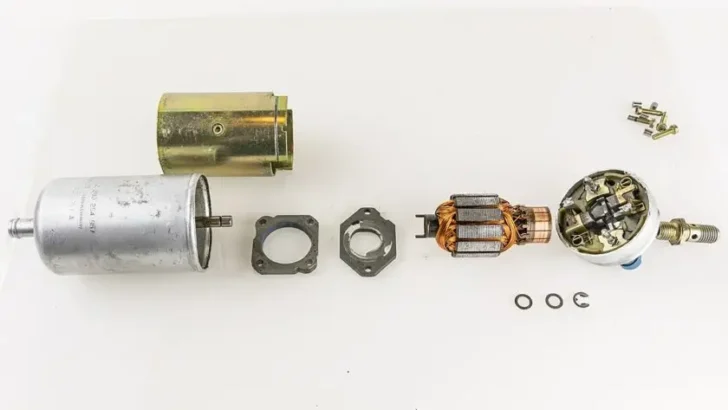
The fuel pump has a function to pressurize the fuel system for the engine to start and then continue providing fuel for the injectors while the engine is running. When you turn on the ignition switch, the ECM PCM activates the pump relay for 2 seconds to turn the pump on and pressurize the system.
If the ECM PCM does not register the engine as running, it will turn off the relay, thus stopping the fuel pump. If the ECM PCM does see the engine running, it will keep the fuel pump running continuously. Some cars are equipped with multi-speed fuel pumps.
These fuel pumps offer more precise control of the fuel supply. In the older type, the ECM PCM varies pump speed by applying either low or high voltage to the pump depending on engine fuel requirements.
When less fuel is needed, the ECM PCM deactivates the fuel pump relay and the current goes through the fuel pump resistor to lower the output of the pump. When fuel demands increase, the ECM PCM activates the fuel pump relay so that current can bypass the resistor and go directly to the pump to increase output.
Late-model cars are equipped with a separate fuel pump control unit (FPCU) that has a function to change the speed of the fuel pump according to the driving conditions.
The fuel pump has three operational speeds: low, mid, and high. When engine speed and load are low, the fuel pump receives 9 volts. Then, as engine speed and load increase, the voltage will increase to 10 volts.
The pump assembly consists of a:
- Strainer pump
- Motor pump
- Impeller relief valve
- One-way check valve
The pump is submerged in the fuel and driven electrically to turn an impeller which will draw fuel through the strainer and develop pressure. The fuel then exits via a one-way check valve.
The purpose of the check valve is to prevent pressure in the fuel rail from flowing back into the tank when the fuel pump is off.
That way, the fuel system will have sufficient pressure when the vehicle is started. The pressure relief valve will open and discharge fuel back into the tank should pressure become excessive.
2. Fuel Pressure Regulator
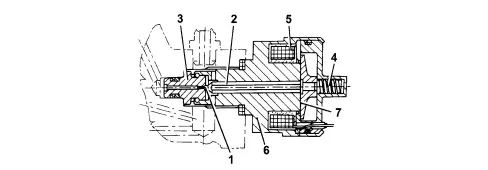
The purpose of the regulator is to keep the fuel at a constant and specific pressure. There are slight differences between the return-type regulator and the returnless-type regulator. The regulator consists of a housing valve, a diaphragm, and a spring. The spring holds the valve closed and allows the fuel pressure to build up against the diaphragm.
When the fuel pressure overcomes the spring pressure, the valve opens and allows excess fuel to bleed off and return to the fuel tank. The regulator on a return-type fuel system is located near the end of the fuel rail.
When the regulator is connected to the intake manifold, a vacuum is routed to the pressure regulator to help overcome the spring force. This is done to maintain constant pressure. The difference between fuel pressure and manifold air pressure.
When the throttle is closed, the manifold vacuum is high and the manifold pressure is low. This results in lower fuel pressure. As the throttle opens, the manifold vacuum decreases while manifold pressure increases. This results in higher fuel pressure.
Regulators that are connected to the intake air duct are not controlled by an engine vacuum. The hose is there to provide unrestricted movement of the regulator diaphragm. These types of regulators operate like returnless regulators where the ECM PCM compensates for changes in intake manifold pressure.
On a returnless type system, the regulator is located in the fuel tank and is part of the fuel tank unit. In order to keep the fuel cooler and to reduce evaporative emissions, the manufacturer placed no return line between the fuel rail and the fuel tank.
3. Fuel Pressure Damper
Some vehicles have a fuel pulsation damper located on the fuel rail. The fuel pressure damper is used to absorb pressure pulses and to reduce noise caused by the injectors opening and closing rapidly. The damper consists of a diaphragm and calibrated spring.
The injectors are opening and close and create a pressure shock wave which is absorbed by the diaphragm as it compresses the spring.
4. Fuel Injectors
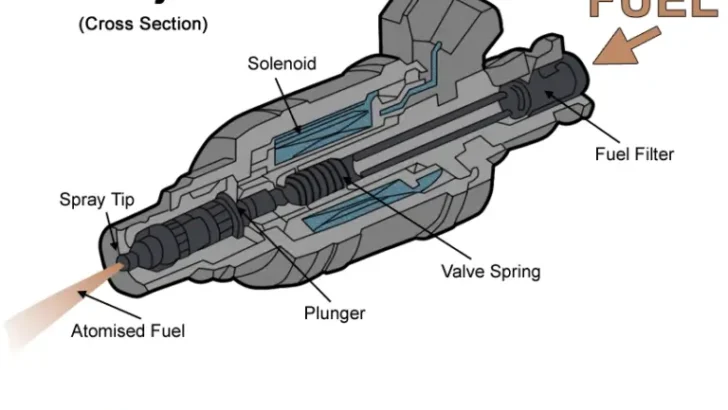
The injector sprays atomized fuel into the intake port of the cylinder. This action is operated electrically. They are normally closed. The ECM/PCM fully opens the injector for a precise time measured in milliseconds in order to deliver the correct amount of fuel to mix with the incoming air.
The longer the fuel injector is in the open position, the bigger amount of fuel is sprayed into the combustion chamber. The fuel injector body is sealed between the intake manifold and the fuel rail.
The internal components of a fuel injector include:
- An inlet screen
- Electrical connector
- Electromagnetic solenoid coil
- Plunger
- A discharge nozzle
The injector discharge nozzle is designed to optimize fuel atomization by creating extremely fine droplets. The improved atomization provides stronger engine performance and reduces emissions .
What Controls The Fuel System?
The fuel system in a vehicle is primarily controlled by the Engine Control Unit (ECU) or Engine Control Module (ECM) in modern vehicles with fuel injection systems.
The ECU is a type of electronic brain that manages various aspects of the engine’s operation, including fuel delivery.
It uses sensors to monitor conditions like engine speed, temperature, and load and adjusts the timing and amount of fuel delivered to the engine accordingly to ensure optimal performance, efficiency, and emissions.
In older vehicles with carbureted systems, the carburetor controls the fuel system, mixing air and fuel in the correct proportions for combustion, with mechanical adjustments needed for different driving conditions.
Troubleshooting The Fuel System
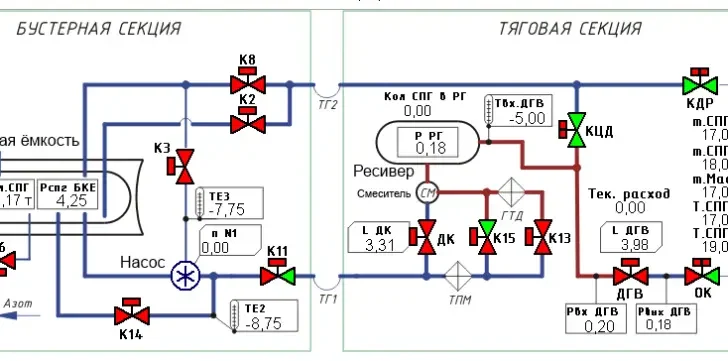
The fuel has to have a constant fuel pressure so the ECM PCM can control the air-fuel ratio accurately. Low fuel pressure can be caused by low or no pump output, a restricted strainer, a restricted filter, a restricted supply line, or a stuck open or weak spring in the regulator.
To isolate which component is responsible for the low-pressure, you can always check for any service bulletins or service news articles that apply and follow the procedures they provide. If there are no bulletins or service news articles, start with the easiest component to test.
1. Inspect the fuel lines
Start by inspecting the fuel lines between the fuel tank and the fuel rail for any leakage, broken pipes, and other damages.
2. Check the pressure regulator
On a return-type fuel system, the pressure regulator would be the next place to start. To determine if the pressure regulator is stuck open relieving too much pressure, the pinch closes the return line with swivel jaw hose pinching pliers. If the pressure rises, the regulator is likely at fault.
3. Replace the fuel filter and strainer suction filter
If the pressure regulator is okay, the fuel filter and strainer suction filter should be replaced. Before you replace them, you need to make sure that whatever condition caused them to become clogged is no longer present.
Otherwise, they may become clogged again soon. If you are working on a returnless fuel system, replace the pressure regulator and fuel filter.
4. Check the fuel pressure
If your vehicle has a long crank time or hard starting, observe the pressure reading right after shutting off the engine. There should not be a rapid fuel pressure drop immediately after shut off.
If the pressure drops fast, the internal possibilities are a check valve in the fuel pump not seating, leaking injectors, pressure regulator not closing, or an external leak such as fuel hoses and lines.
5. Test the injectors
Remove the fuel rail and injectors together and check for leaks by turning the ignition switch on. You can also check for leaky injectors by pinching off both the fuel inlet and return lines and then monitoring fuel pressure.
6. Inspect the fuel pump check valve
If the injectors are ok, then the fuel pump check valve is the issue and the pump will need to be replaced. Note that the check valve is an integral part of the fuel pump and cannot be separately replaced.
7. Look for restrictions in the return line after the regulator
High fuel pressure can be a result of a faulty regulator or a restriction in the return line after the regulator. Check the vacuum hose to the regulator first. If it is disconnected or blocked from the manifold vacuum, the pressure will be high. If you see fuel in the vacuum line, the pressure regulator diaphragm is leaking and needs to be replaced.
Fuel Delivery System Operation
Like other electrical components on the vehicle, the fuel pump and injectors require power to operate. But, they don’t just operate all the time. Instead, they are controlled by the ECM PCM through relays to operate at the correct time.
A relay is an electromagnetic switch that has two sides: power and control. The ECM PCM operates the control side of the relay to provide a power path to the fuel injectors and the fuel pump. Fuel injectors are on/off solenoid valves that spray fuel into the intake port of the cylinder. The fuel injectors require power and ground to operate.
The power to the injectors comes through the PGM-FI main relay which is energized whenever the ignition switch is turned on. The ECM PCM provides the injectors with a ground path. This is also how it turns the injectors on and off.
When there is no ground, the injector is closed and is not spraying fuel. When there is ground, the injector is open and spraying fuel. The longer the ground is on the longer the injector is open and the more fuel that enters the combustion chamber.
The ECM PCM uses various inputs to calculate exactly when the grounding injector opening time should begin and how long it should last. The opening time is called ”injector duration” and is measured in milliseconds-thousandths of a second.
A vehicle decelerates with a closed throttle. The ECM PCM turns the fuel injectors off to save fuel and it turns the injectors back on right before the engine reaches idle speed.
This function is called ”fuel cut” and is normal. Fuel cut-off also occurs when engine speed gets too high regardless of the throttle position. It does this to protect the engine from over-revving.
FAQs
Q: What is the function of the fuel system?
A: The fuel system is responsible for storing, delivering, and supplying fuel to the engine of a vehicle.
Q: How does the fuel system work?
A: The fuel system works by drawing fuel from the fuel tank, pumping it through the fuel lines, and delivering it to the engine where it is mixed with air and ignited to produce power.
Q: What are the components of a fuel system?
A: The main components of a fuel system include a fuel tank, fuel pump, fuel injector, fuel filter, fuel pressure regulator, and fuel lines.
Q: What is the purpose of a fuel tank?
A: The fuel tank is a storage container that holds the fuel until it is needed by the engine.
Q: What is fuel injection?
A: Fuel injection is a system that electronically controls the amount of fuel that is delivered to the engine.
Q: What are the different types of fuel injection systems?
A: There are two main types of fuel injection systems: electronic fuel injection (EFI) and mechanical fuel injection.
Q: What is the role of a fuel pump?
A: The fuel pump draws the fuel from the tank and pumps it to the engine.
Q: How does a mechanical fuel injection system work?
A: In a mechanical fuel injection system, the fuel is delivered to the engine through mechanical means, such as a series of mechanical pumps and valves.
Q: What are the symptoms of a bad fuel system?
A: Symptoms of a bad fuel system can include poor fuel economy, engine misfires, difficulty starting the engine, and a decrease in overall vehicle performance.
Q: How can I clean the fuel system?
A: To clean the fuel system, you can use fuel system cleaning additives that are specifically designed to remove deposits and improve fuel efficiency.
In Conclusion
The fuel tank and fuel system are integral components of a vehicle’s engine.
Fuel tanks provide the necessary fuel storage for the engine, while the fuel system delivers this fuel to the chambers where it is burned for energy.
Modern vehicles have complex systems with sophisticated controls that keep the engine running efficiently and effectively.